L’utilizzo dei compositi avanzati nella nautica da diporto: le fibre di carbonio
Come tutti ben sanno, la stragrande maggioranza delle imbarcazioni da diporto viene realizzata con la Vetroresina che è quel materiale ottenuto dall’insieme di fibre di vetro e resine termoindurenti.
In realtà, negli anni, anche l’industria nautica ha registrato una serie di “avanzamenti” in termini di sviluppo.
Se ci riferiamo alle resine (ossia alla fase fluida che una volta indurita tiene insieme le fibre), ad esempio, non sono pochi i Cantieri che sono passati gradualmente dall’utilizzo di matrici meno pregiate (come le polisteri – isoftaliche) a quello di resine più performanti (sia meccanicamente che sotto il profilo fisico-chimico) come le vinilesteri.
Non solo: facendo un altro passo in avanti, alcuni Cantieri da diporto hanno addirittura iniziato ad attrezzare reparti dove viene lavorata l’epossidica (non più, pertanto, relegata solamente alle imbarcazioni da competizione) che offre garanzie ancora superiori rispetto alle vinilesteri anche se poi richiede più accuratezza (ammette meno possibilità di errore) nella lavorazione.
Sotto il profilo tecnologico, allo stesso modo, si è progredito. Ormai è più di un decennio che molti Cantieri nautici hanno iniziato a produrre con tecnologie sotto-vuoto (come l’infusione) che garantiscono, oltre a migliori condizioni di lavoro, elevate performance in termini di resistenza specifica e minor spreco di matrice.
Inoltre, sempre gradualmente (ma progressivamente), diverse realtà hanno iniziato ad introdurre nelle “distinta base” dei propri manufatti le famigerate fibre di carbonio, croce e delizia di progettisti che cercano “alte prestazioni”.
Ma cerchiamo un attimo di capire cosa sono questi particolari tipi di fibra.
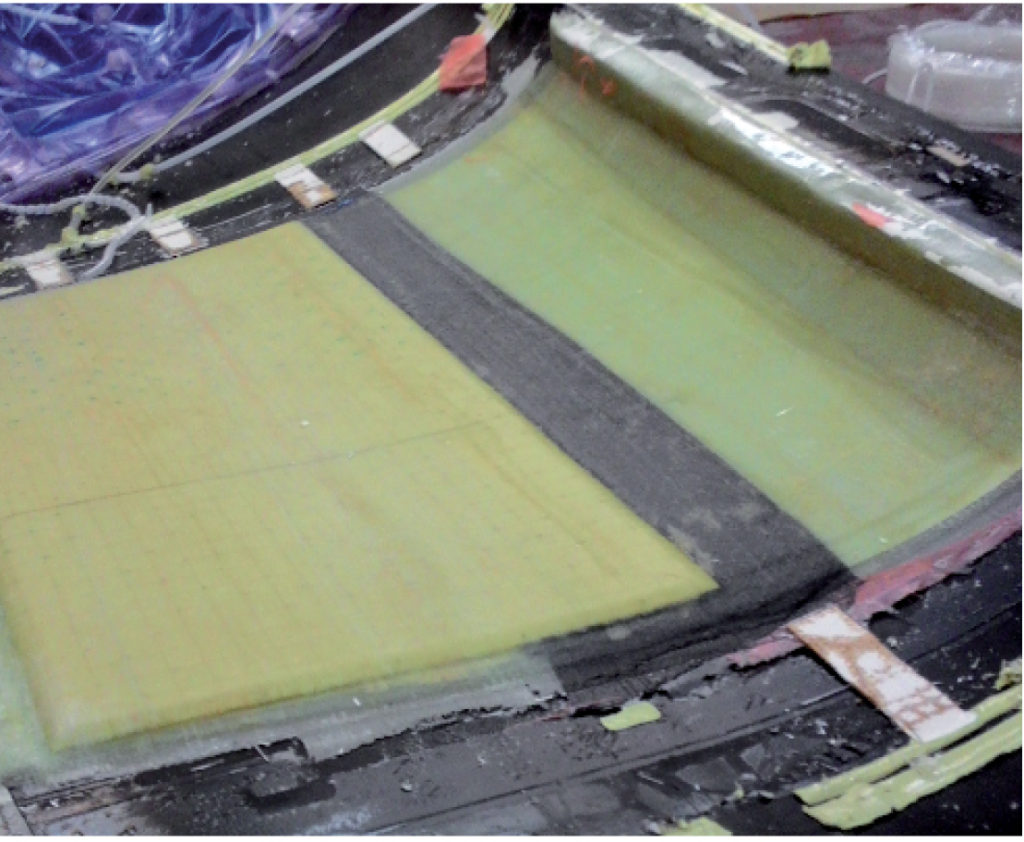
su un pannello campione
Innanzitutto iniziamo col dire che le fibre di carbonio, scoperte intorno al 1880 da Edison, sono state prodotte commercialmente intorno agli anni ’60 del secolo scorso. Le applicazioni per cui questo tipo di rinforzo nasceva, viste le alte proprietà meccaniche che le caratterizzano, sono state per molti decenni prevalentemente incentrate in ambito aero-spaziale ed aeronautico in generale.
Inizialmente i costi erano proibitivi per poter pensare ad applicazioni più comuni e, pertanto, sono rimaste relegate davvero ad un ruolo di nicchia per molto molto tempo.
Tutto sommato, man mano che venivano prodotte e si affinavano i processi di sintesi (dal PAN o dalla Pece), i costi diventavano (relativamente) più accessibili e si cominciava a pensare ad esse anche per applicazioni non strettamente connesse col settore “militare”.
Oggigiorno, in realtà, l’utilizzo non è ancora diffuso su larga scala sebbene possiamo dire che l’industria dell’automotive, delle attrezzature sportive e delle imbarcazioni da competizione cominciano a farne un discreto utilizzo.
Il diporto nautico, nello specifico, seppur timidamente comincia anch’esso ad inserire strati di fibra di carbonio all’interno di laminati di vetro, ottenendo – pertanto – una buon miglioramento in termini di proprietà (e di riduzione di peso) senza far lievitare troppo i costi di produzione.
Purtuttavia, nonostante la diffusione di cui parlavo, noto ancora una certa confusione quando si tratta questo argomento e constato talvolta un utilizzo non “ad hoc” del materiale in questione.
Cosa voglio dire con questa affermazione? Tralasciando il lato “trendy” dell’uso del Carbonio è bene avere un minimo di consapevolezza quando si decide di integrare questo rinforzo con i più classici tessuti di vetro.
Cominciamo, pertanto, con il confronto di alcune proprietà.
Senza entrare in discorsi troppo ingegneristici, poco comprensibili ai più, iniziamo a parlare del primo parametro: la Massa Volumica.
Affinché sia chiaro il più possibile facciamo un parallelo con una sostanza che tutti conosciamo: l’acqua. Ebbene, se immaginiamo di riempire d’acqua un cubo di vetro, di lato pari 1 m, questo cubo peserebbe esattamente 1000 kg.
Facendo lo stesso esperimento (immaginando di compattare al massimo le fibre) col Carbonio, il cubo in questione peserebbe soltanto l’80% in più del cubo di acqua, ossia circa 1800 kg.
Se lo facessimo con le fibre di vetro otterremmo un peso di circa 2700 kg (come l’alluminio approssimativamente), mentre se lo riempissimo di acciaio peserebbe 7850 Kg! Capiamo, pertanto, quanto sia “leggero” il Carbonio se confrontato con altri materiali come possono essere le stesse fibre di vetro (2700 kg/mc vs 1800 kg/mc) e l’acciaio (7800 kg/mc vs 1800 Kg/mc).
Ma guardiamo ora anche alla “resistenza meccanica alla trazione”. Cerchiamo di comprendere attraverso qualche esempio prendendo spunto dalla tabella sottostante:
Se guardiamo l’ultima colonna sulla destra, leggiamo che la “Resistenza Meccanica” dell’Acciaio è pari a 540 Mpa (Mega Pascal).
Tradotto: l’acciaio resiste ad una forza applicata (per ogni millimetro quadrato) di ben 55 kg!
Ma guardiamo il carbonio. Nella tabella sono riportate tre tipologie (alta resistenza, alto modulo, altissimo modulo). Guardiamo per comodità il terzo tipo di carbonio (quello a “bassa” resistenza). Possiamo leggere che esso ha una “Resistenza Meccanica” che è pari a 1500 MPa. Tradotto: il carbonio resiste ad una forza applicata (per ogni millimetro quadrato) di circa 150 kg (tre volte superiore a quella dell’acciaio)
Bene, fatte queste premesse, è anche corretto dire che si sta facendo riferimento a valori teorici della fibra di carbonio in un’unica direzione (quella del carico).
Pertanto, è giusto affermare che queste proprietà non sono facilmente raggiungibili, se non altro perché comunque in ogni composito il carbonio “compartecipa” alle proprietà meccaniche del laminato: l’altra parte deriva dalla resina (che è trascurabile se confrontata con questi valori).
Ma allora come si fa a predire le proprietà meccaniche della carena, piuttosto che del boma o dell’albero?
Ebbene, premettendo che occorrono fior di specialisti per poter fare questi tipi di calcoli, farò un esempio molto semplice.
Supponendo che un albero sia costituito da fibre di carbonio monodirezionali impregnate con resina epossidica e che il rapporto carbonio/resina sia pari al 50 %, la resistenza meccanica dell’albero sarà banalmente pari alla metà del valore teorico di tabella, ossia: 1500 Mpa x 0,5 = 75 kg/mmq.
Quindi, il nostro albero (con fibre di carbonio tutte allineate lungo la direzione del carico) avrà una resistenza ancora superiore a quella dell’acciaio (di circa il 50%) ma con un peso largamente più basso (del 70 % inferiore, per la precisione !)
Ed ecco spiegato, in brevi e poveri passaggi, l’utilizzo del Carbonio all’interno di compositi ad alta prestazione.