La costruzione sandwich nelle imbarcazioni da diporto
Nella nautica da diporto si parla genericamente di vetroresina, anche se questo termine designa una classe di materiali molto ampia. Grazie alle numerose possibilità di combinare resine, fibre, materiali d’anima ed inserti, la vetroresina può assumere caratteristiche molto diverse. Questa peculiarità la rende adatta per costruire un’imbarcazione planante o un gozzo dislocante, una tavola da surf, una canoa o anche un pattino da spiaggia.
Parliamo della costruzione sandwich nelle imbarcazioni da diporto.
VETRORESINE E MATERIALI D’ANIMA
Le possibilità applicative di questo complesso materiale sono davvero molto ampie e consentono ai progettisti di realizzare un materiale dimensionato “ad hoc” per ogni esigenza.
Anche all’interno dello stesso progetto, si possono avere “vetroresine” differenti perché composte da fibre di diversa tipologia, grammatura, orientazione. Oppure possono essere resine chimicamente non uguali, in base allo scopo o all’applicazione.
Ad esempio, resine che presentano maggiore resistenza all’acqua, resine ignifughe o resistenti agli idrocarburi.
Analogamente, la possibilità di spaziare è molto ampia anche per i materiali d’anima. Si tratta delle schiume polimeriche che solitamente noi progettisti inseriamo all’interno dei laminati per conferire grande resistenza alla deformazione, non appesantendo oltre modo la scocca dell’imbarcazione.
In questo articolo passeremo in rassegna questa tipologia di materiale. Faremo chiarezza sulle principali tipologie e caratteristiche necessarie per essere inserito nella scheda di laminazione di ogni imbarcazione.
NON SONO TUTTI UGUALI
Esistono nel mondo vari produttori di materiali d’anima. Tuttavia io ritengo che sia conveniente affidarsi a produttori di primaria importanza, che lavorino in regime di qualità e che abbiano nel proprio catalogo materiali di prima scelta, con caratteristiche tecniche chiare e pesi controllati.
Nel mondo non specialistico, erroneamente, si tende a ritenere “simili” tutti questi materiali, anche se in realtà progettare un laminato sandwich non è assolutamente facile.
Anzi, la progettazione sandwich è una branca di quella con i materiali compositi, che segue una serie di leggi matematiche ed algoritmi tutt’altro che semplici.
Ne consegue che il progetto ottimizzato di un’imbarcazione dovrà tenere conto non solo del giusto numero di strati di vetro e della tipologia adatta di resine, ma anche del corretto spessore dell’anima, in funzione della zona in cui viene utilizzata e della corretta massa volumica.
Inoltre, bisogna integrare con cognizione di causa tutte le proprietà meccaniche della schiuma con quelle delle fibre e delle resine.
In parole molto molto semplici, i “Core Material” vengono impiegati per ottenere una grande resistenza alla deformazione, senza alterare il peso dell’imbarcazione.
Essi possono essere usati con ogni tipologia di fibra, carbonio compreso.
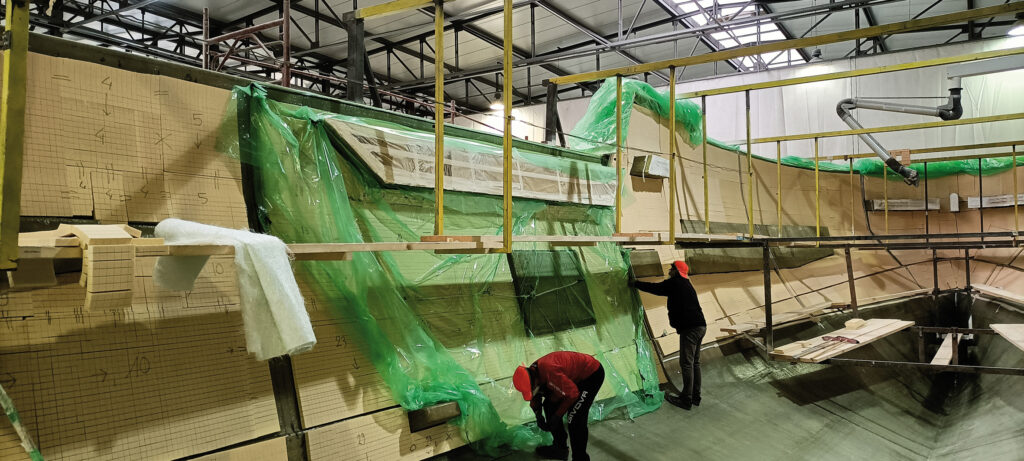
che incolla rigorosamente sottovuoto nel rispetto dell’ambiente e delle migliori performance tecniche
IL CARBONIO NON SEMPRE È LA RISPOSTA
L’utilizzo del famigerato carbonio, infatti, non garantisce da solo una “rigidezza flessionale” che possa sopportare ogni tipo di sollecitazione.
È complesso, in un articolo divulgativo che ha una platea di lettori molto variegata, spiegare il perché di questa mia “strana” affermazione, ma voglio comunque provarci.
Una lamina di carboresina di pochi millimetri di spessore sarà estremamente resistente se la tiriamo fra due punti, potrà quindi esibire una resistenza in trazione superiore agli acciai comuni.
Tuttavia sotto un carico ad essa perpendicolare – immaginiamo un grosso elefante al centro di questa lamina in carbonio – tenderà a deformarsi in maniera importante fino, probabilmente, a rompersi.
Questo fenomeno di estrema deformazione (che a sua volta può portare alla rottura del laminato), tuttavia, può essere arginato se la bandella di carbonio viene laminata al di sopra e al di sotto di un’anima di PVC espanso (da qui, la definizione di “composito Sandwich“) con il corretto spessore, la calcolata massa volumica e lo specifico modulo di taglio.
La rigidezza flessionale di un materiale deriva, infatti, oltre che dalle proprietà intrinseche dei materiali stessi (e quindi materiali come il carbonio contribuiscono assolutamente alla capacità dell’imbarcazione di non deformarsi sotto carichi anomali), anche dallo spessore del laminato e l’aumento di tale parametro con i materiali d’anima consente di garantire leggerezza alla scocca.
PERCHÉ NON LE FIBRE DI VETRO
Qualcuno potrebbe obiettare che lo spessore può essere raggiunto tranquillamente aggiungendo strati di vetro, come si faceva alcuni decenni fa su molte imbarcazioni per aumentarne la rigidezza flessionale.
Sempre per rimanere in ambito di semplice spiegazione non accademica, posso rispondere a questa obiezione dicendo che aggiungere strati di fibra di vetro per ottenere l’aumento delle proprietà inerziali è antieconomico e può essere uno svantaggio tecnico.
Basti pensare, sempre per fare esempi pratici e concreti, che se volessimo aumentare lo spessore con fibre di vetro e resina, avremmo come conseguenza delle imbarcazioni pesantissime e ciò comporterebbe una serie di svantaggi, come scarse performance della barca ed elevata incidenza dei consumi di carburante.
Sempre per dare un’idea: una lastra quadrata di vetroresina da un metro di lato ed un centimetro di spessore può pesare anche dalle dodici alle quindici volte in più rispetto ad una lastra di materiale d’anima (mediamente).
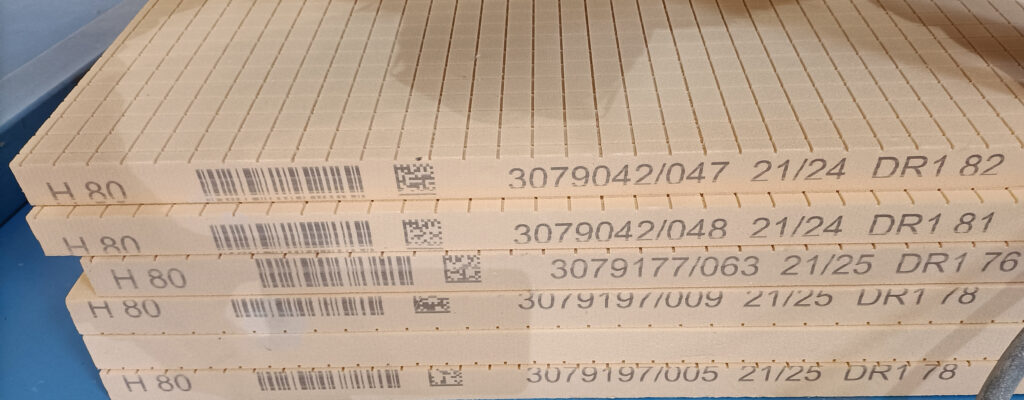
In questa foto possiamo notare la finitura che lo rende adatto per la tecnologia di infusione
CORE SINTETICI E NATURALI
Detto questo, le aziende come DIAB producono essenzialmente tre tipi di CORE.
Due sono di origine sintetica, ed una naturale.
Le anime di origine naturale sono quelle di balsa e derivano da latifondi arborei dell’America Latina che, fra l’altro, risultano anche di complessa reperibilità ed elevato costo. La maggior parte dei progettisti, in realtà, preferisce per diverse ragioni le schiume sintetiche come il PVC ed il PET.
Le prime, ossia le anime di PVC, sono quelle che storicamente vengono adottate prevalentemente nella nautica da diporto.
Al giorno d’oggi, la quasi totalità dei progettisti utilizza il PVC sui ponti di coperta, su tutti i particolari (dai roll-bar, agli hard-top, fino al mobilio) e nelle murate degli scafi.
Laddove, invece, sono richieste importanti performance di velocità, resistenza e leggerezza, si può inserire il PVC anche nell’opera viva di carena, conseguendo – pertanto – una costruzione cosiddetta “full-sandwich”.
Il PET, invece, è un materiale relativamente più “giovane” rispetto al PVC. Nella nautica, a dire il vero, non ha ancora una larga applicazione, sebbene molti cantieri e costruttori inizino a chiedere informazioni su questo innovativo materiale per alcune sue caratteristiche, come la riciclabilità e la resistenza al fuoco.
In questi mesi, si stanno portando avanti studi comparati dove il PET viene accoppiato a fibre di basalto e a resine termoplastiche.
Lo scopo è quello di certificare, al più presto, un materiale completamente eco-friendly e chissà – magari – che la prima barca sandwich totalmente riciclabile venga prodotta proprio nel nostro Paese.
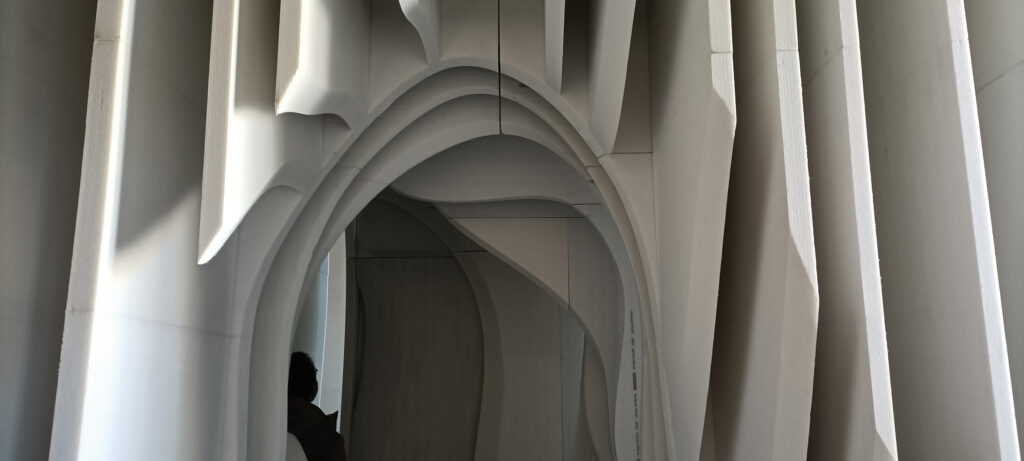
di ingresso dell’università NAU (Nature Architecture University) in virtù delle sua eco-sostenibilità
DOTT. GIUSEPPE COCCIA
Ingegnere industriale, laureato con lode presso l’Università di Napoli Federico II.
Specialista in Materiali Compositi, ha conseguito un Dottorato di Ricerca in Tecnologie e Sistemi Intelligenti per l’automazione della Produzione.
Esperto internazionale sulla tecnica di stampaggio per infusione sottovuoto, è stato relatore e chairman a numerosi congressi e conferenze in Italia, Francia e Stati Uniti. Pubblica periodicamente, su riviste tecniche italiane e straniere, articoli in materia di imbarcazioni e relative tecnologie di costruzione.
È stato Direttore della Produzione e Dirigente Tecnico per diversi Cantieri Nautici.
Attualmente è titolare dello Studio Tecnico Ing. Coccia che svolge consulenze e perizie nel settore Nautico e Compositi.