FIM 440 Regina, inaugurazione del nuovo sito produttivo e intervista ai fondatori
Presentato il concept del nuovo FIM 440 Regina. Ma non è l’unica novità in casa FIM. La costante crescita della produzione, a seguito dei continui successi riscossi nel mercato italiano e internazionale, ha portato il cantiere bergamasco a insediarsi in un nuovo sito produttivo all’interno di un vero e proprio Polo Nautico, situato a Cividate al Piano, in un’area geograficamente strategica vicino a Bergamo.
Il cantiere FIM, acronimo di Fabbrica Italiana Motoscafi, nasce nel 2019 dalla passione e dalla ventennale esperienza maturata all’interno della filiera produttiva nautica dei loro fondatori, Corrado Piccinelli e Manuela Barcella, ai quali si unisce il socio investitore Vannis Marchi, imprenditore di successo e co-fondatore del noto brand di moda Liu Jo, che sostiene le scelte e i progetti del cantiere facendosi promotore del suo sviluppo nel mercato nautico internazionale.
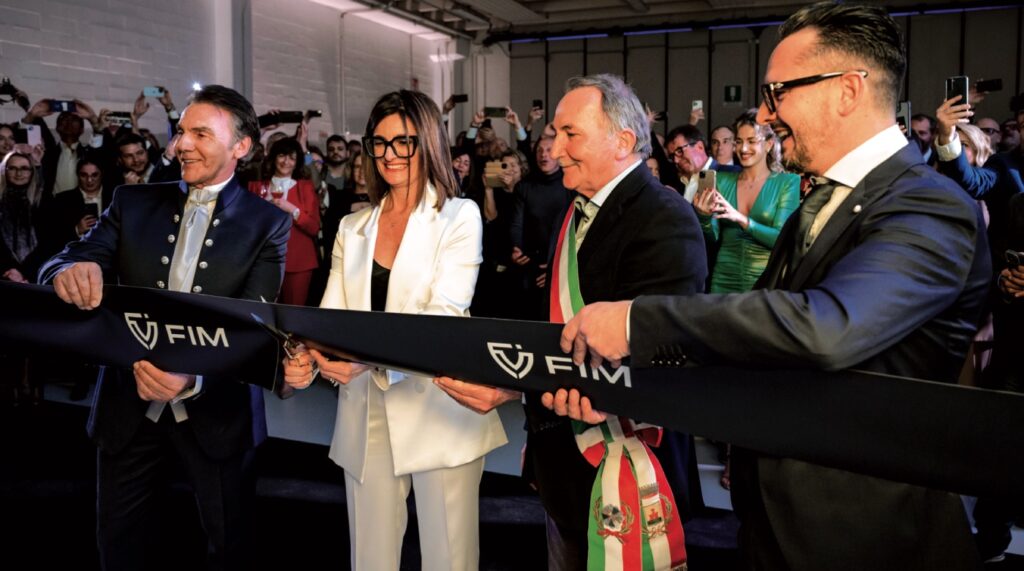
In occasione dell’inaugurazione del nuovo sito produttivo, abbiamo avuto modo di intervistare i fondatori del cantiere per scoprire come vengono prodotte le imbarcazioni FIM all’interno del Polo Nautico di Cividate al Piano.
***
Quando vi siete trasferiti nel nuovo sito produttivo e quanta superficie occupa?
Ci siamo trasferiti nell’ottobre 2022, dopo aver acquisito questa area produttiva di più di 5.000 mq di superficie coperta, a cui si aggiungono 1.000 mq di magazzino e 800 mq di uffici, all’interno di un vero e proprio Polo Nautico che si estende su una superficie di 20.000 mq. Gli altri immobili del Polo sono stati acquistati dal nostro socio, il Sig. Vannis Marchi.
In occasione dell’inaugurazione del nuovo cantiere, ci potete svelare i vostri prossimi progetti? Qual è, inoltre, la massima dimensione d’imbarcazione che sarà possibile produrre nel nuovo sito e con quale capacità produttiva?
Nei prossimi 4 anni abbiamo un programma di sviluppo della nostra gamma con l’obiettivo di produrre un modello nuovo all’anno. Quest’anno presentiamo il 440 Regina, una barca sportiva; per il prossimo anno realizzeremo un 58 piedi sia in versione coupè che sport fly. Successivamente sarà la volta di un 55 piedi sport fly e completeremo la gamma con l’ammiraglia flybridge da 65 piedi. Questo sito produttivo è stato realizzato e strutturato per la produzione di imbarcazioni fino a 65 piedi di lunghezza. A regime, la capacità produttiva sarà tra le 50 e le 55 barche all’anno.
Come nasce e come si sviluppa il progetto di una barca FIM?
Quando pensiamo alla creazione di una nuova barca, ci avvaliamo della collaborazione di professionisti per lo sviluppo dei progetti. Pensiamo che affidarsi a studi professionali specializzati nelle diverse fasi di studio e di industrializzazione di un progetto possa farci raggiungere migliori standard qualitativi, oltre a velocizzare le tempistiche. Collaboriamo quindi con studi di design per dare forma alle nostre idee, sia per plasmare le linee estetiche della barca che per realizzare gli ambienti e gli arredi.
Altri professionisti realizzano e certificano i progetti degli impianti di bordo. Per quanto riguarda lo sviluppo delle carene, siamo seguiti da un ufficio tecnico di Roma, leader nello studio delle linee d’acqua delle opere vive degli scafi attraverso progetti supportati da calcoli computerizzati con software di analisi fluidodinamica. Vengono quindi realizzate le matematiche delle varie parti della barca per l’industrializzazione, con lo studio dei volumi, della distribuzione dei pesi e simulazioni dell’assetto. Il tutto avviene sempre a stretto contatto e sotto la supervisione dello staff del nostro ufficio tecnico interno.
Una volta approvato l’intero studio del progetto, si passa alla realizzazione degli stampi dello scafo, delle sovrastrutture e degli hard top. Dalle matematiche create a computer delle varie parti della barca, gli stampi vengono realizzati mediante l’utilizzo di fresatrici a controllo numerico.
Come avvengono le fasi di stampaggio e quali materiali utilizzate?
Dopo il trasferimento nel Polo Nautico di Cividate al Piano, abbiamo realizzato una unità produttiva strutturata per lo stampaggio degli scafi, delle sovrastrutture e degli hard top del 34 piedi, FIM 340 Regina, e del nuovo FIM 440 Regina. All’interno di questa unità produttiva, i manufatti vengono stampati da terzisti specializzati, seguendo i nostri protocolli. Abbiamo quindi modo di controllare direttamente le fasi di stampaggio e la qualità delle stampate.
Dopo aver spruzzato il film di gelcoat sulle pareti dello stampo, lo stampaggio avviene mediante laminazione manuale della vetroresina in single skin, utilizzando resina vinilestere. In fase di stampaggio, la carena viene strutturata inserendo il ragno di rinforzo in espanso, laminato al resto dello scafo. Con lo stesso procedimento si vanno a finire le parti dei manufatti che richiedono un rinforzo strutturale. Gli hard top sono invece laminati in fibra di carbonio in modo da contenere i pesi.
Una volta estratto dallo stampo, il manufatto viene portato all’interno di una cabina climatica in grado di trattare 40.000 metri cubi d’aria ogni ora controllando temperatura e umidità secondo profili ben precisi e programmati al computer, per eseguire il “post curing” dello stampato. Il manufatto viene tenuto nella camera climatica per circa 7-8 ore seguendo cicli termici che raggiungono la temperatura di 85-90 °C in modo da controllare la fase di polimerizzazione della vetroresina, stabilizzando la stampata a favore della qualità finale.
Una volta effettuate le finiture manuali sul manufatto ed eventuali ritocchi di carrozzeria, nella stessa cabina si esegue la verniciatura. Seguendo profili termici programmati riusciamo ad aumentare la qualità di fissaggio della vernice e migliorare la sua tenacia all’aggressione degli agenti atmosferici. La cabina climatica e di verniciatura del nostro cantiere ha una lunghezza di 15 m, una larghezza di 8 m e un’altezza di 6 m ed è dotata di doppia porta con la possibilità di essere allungata in futuro. Al suo interno è possibile quindi lavorare scafi fino a 50 piedi con baglio di 5 m.
La programmazione di differenti profili termici nella cabina ci permette di sperimentare vari tipi di vernici sia a solvente che ad acqua.
Per quanto riguarda la nostra attuale ammiraglia, il 470 Regina, scafo e coperta vengono stampati da un terzista specializzato in una struttura al di fuori del Polo Nautico, seguendo i nostri protocolli e i severi controlli di qualità. Stiamo già studiando il nuovo modello di 58 piedi che verrà stampato con il processo d’infusione.
Come sono organizzate le linee di produzione nel nuovo cantiere?
In cantiere abbiamo maestranze specializzate per ogni singolo modello della gamma. Ogni squadra produrrà quindi sempre lo stesso modello in linea di produzione, certi che questa organizzazione porti a migliorare la qualità globale delle nostre barche. Altre maestranze del cantiere preparano i semilavorati tra cui i quadri elettrici, le plance con l’elettronica di bordo, i kit degli impianti idraulici e i precablati. Nella linea di produzione di un’imbarcazione vengono impiegate 7-8 maestranze, tra le quali alcune sono specializzate nell’allestimento dello scafo e altre nella realizzazione del ponte di coperta e delle sovrastrutture. In ciascuna linea di produzione divisa per modello, l’allestimento del ponte e dello scafo vengono portati avanti in parallelo, seguendo procedure e protocolli specifici.
Il direttore di produzione controlla ogni settimana lo stato di avanzamento dei lavori insieme al responsabile del controllo qualità.
In cantiere abbiamo un reparto di carrozzeria pronto a effettuare ritocchi e finiture durante le fasi di avanzamento dei lavori, mentre gli addetti al reparto di falegnameria preparano i grezzi da montare nello scafo e le strutture dei cielini.
L’allestimento dello scafo viene effettuato a “cielo aperto” in modo da poter agevolare la realizzazione degli impianti elettrici e idraulici, l’alloggiamento dei serbatoi, l’approntamento della sala macchine, la posa delle paratie e degli arredi interni voluminosi. Una volta terminato l’allestimento di scafo e coperta, la linea di produzione è pronta per eseguire l’assemblaggio delle due parti. È un passaggio delicato che il cantiere esegue con massima cura, in modo da creare un solido monolite che mantenga la qualità costruttiva nel tempo. Per questo motivo scafo e coperta sono uniti con un collante strutturale lungo il perimetro, che viene successivamente rivettato dall’esterno ogni 20 cm e fascettato dall’interno con vetroresina, realizzando una triplice sicurezza nell’assemblaggio.
Una volta ultimate le finiture degli interni, dai rivestimenti alle tappezzerie, gli arredi e tutta l’impiantistica, la barca viene portata in vasca di collaudo dove vengono provati i motori, gli impianti e l’assetto. Successivamente, sempre in vasca, si effettuano i controlli di infiltrazione sottoponendo la barca a 3 ore di doccia intensiva. Al termine dei collaudi e del controllo qualità, l’imbarcazione viene trasferita nell’area di finitura e pulitura per la consegna.
Una volta ricevuto l’ordine di una barca, come viene organizzata la preparazione dei materiali e della componentistica per la produzione, pensando anche alle esigenze del servizio post-vendita?
L’ordine di un’imbarcazione viene ricevuto dal nostro ufficio commerciale, composto da 2 addetti, i quali attraverso un apposito software creano una scheda imbarcazione con una distinta base dettagliata che include le caratteristiche e gli optional richiesti dal cliente. Dopo essere stata visionata e approvata dall’ufficio tecnico per validare eventuali customizzazioni, la scheda imbarcazione passa all’ufficio acquisti per verificare che tutta la componentistica e gli optional inseriti nella distinta base siano disponibili in magazzino, uno dei reparti nevralgici del cantiere.
Abbiamo infatti diversi fornitori di componenti, dagli elementi in acciaio inox, ai mobili d’arredo, alle cuscinerie e tappezzerie, ai serbatoi e tutte le parti degli impianti idraulici ed elettrici di bordo. Per questo motivo tutti i componenti, i semilavorati e i kit relativi agli optional, sono codificati con bar code in modo da caricare nel software i componenti quando entrano in magazzino e scaricarli quando vengono prelevati per la produzione. In questo modo è possibile monitorare costantemente via software la giacenza del magazzino; cerchiamo sempre di tenere uno stock adeguato in modo da rispettare tempi congrui di consegna per il cliente. Il nostro magazzino occupa una superficie di circa 1.000 mq ed è gestito da 3 addetti. Quando la distinta base della scheda imbarcazione arriva in magazzino, gli addetti prelevano tutti i componenti, i semilavorati e i kit, scaricando i relativi codici nel software, portando successivamente il tutto in linea di produzione. Attraverso la codifica dettagliata, si ottiene la tracciabilità dei componenti e dei kit montati sulla barca, che è possibile consultare nella distinta base via software.
È un sistema molto pratico e funzionale pensato e messo a punto anche per le esigenze del service post-vendita. Per FIM è infatti molto importante prendersi cura del cliente attraverso un efficiente servizio post-vendita. Per questo motivo le nostre imbarcazioni sono realizzate in modo che i punti di ispezione degli impianti siano facilmente raggiungibili e, in particolare, che tutta la componentistica di bordo sia tracciabile attraverso codifiche precise per la consultazione, abbinate a documentazioni tecniche e schemi chiari, con lo scopo di ridurre i tempi per le manutenzioni o per le eventuali risoluzioni dei guasti.
***
Sfoglia per continuare a leggere i dettagli del nuovo FIM 440 Regina