I principi fondamentali dell’infusione sottovuoto – I parte
Ancora oggi, capita che vengano posti quesiti apparentemente banali sull’utilizzo dell’infusione per la costruzione delle imbarcazioni.
Le domande possono essere poste o da armatori che si avvicinano all’acquisto o dagli uffici tecnici di cantiere che iniziano a valutare la fattibilità del progetto industriale.
“A cosa serve, fondamentalmente, l’infusione sottovuoto? Com’è nata?”, “Le tecnologie sottovuoto sono meglio della laminazione manuale?”, “La qualità migliora? In caso affermativo, su quale aspetto?”, “L’imbarcazione infusa è più leggera? E se sì, di quanto?”, “Si recuperano ore di manodopera?”, “E’ possibile immaginare che si economizzi sul carburante?”, “Il processo industriale costa meno?”, “E’ costosa la sua industrializzazione?”
Tutte domande legittime, a cui, a mio parere, non possono essere fornite risposte univoche ed insindacabili poiché dipendono da molteplici “condizioni al contorno”.
I tecnici che offrono soluzioni senza valutare attentamente le possibili variabili o sono in mala fede o, peggio ancora, non sono troppo competenti in materia.
In questo editoriale, pertanto, si cercherà di fare un minimo di chiarezza all’interno di un argomento complesso ed oggetto – ancora oggi – di dibattiti e discussioni: l’infusione sottovuoto.
Non pensiamo, in realtà, che tutti i dubbi o le perplessità relativi a questa tecnica possano essere risolti nel giro di qualche pagina di editoriale, ma riteniamo tuttavia che qualche certezza, dopo ormai due decenni di lavoro costante svolto all’interno delle produzioni di molteplici cantieri, possa essere raggiunta.
SOLVENTI ORGANICI VOLATILI (SOV)
Partiamo con l’affermare una verità di fondo (a cui l’armatore medio può non essere necessariamente sensibile), legata alla sicurezza dei luoghi di lavoro e alla salute degli operatori: le tecniche di lavorazione sotto-vuoto sono maggiormente “eco-friendly” rispetto alle tecniche manuali in “stampo aperto” (ossia la classica stratificazione delle imbarcazioni).
Durante il processo di “deposizione manuale”, infatti, viene liberata nel luogo di lavoro una serie di solventi (fra cui il famigerato stirene per il quale una Direttiva Europea ha stabilito le massime concentrazioni consentite nell’ambiente) che sicuramente non possono essere definiti “salutari” per l’operatore.
Nelle tecniche “sottovuoto” (e fra queste possiamo includere nell’alveo delle tecnologie nautiche oltre all’infusione, anche l’RTM e la compattazione sotto sacco), invece, i solventi volatili restano “intrappolati” all’interno del sacco che sigilla lo stampo dello scafo, della coperta o delle controstampate.
Per tale motivo, anche se il problema dei SOV non è stato ancora risolto al 100%, con l’infusione (ed in generale con le tecniche sottovuoto) può essere comunque drasticamente abbattuto.
Molti, ormai, sono gli studi e le ricerche dimostranti che l’utilizzo massivo dell’infusione riporta il cantiere costruttore di imbarcazioni all’interno dei parametri di emissione consentiti dalle direttive europee.
Quindi, come primo importante punto, possiamo affermare che l’infusione sottovuoto abbatte drasticamente le concentrazioni dei solventi organici volatili nell’ambiente di lavoro e consente al cantiere costruttore di allinearsi più facilmente alle indicazioni di legge relative.
RIPETIBILITÀ DEI RISULTATI
Un altro punto fondamentale relativo alle tecniche di lavorazione “sottovuoto” è legato al grado di ripetibilità dei risultati. Sicuramente un cantiere costruttore che opera con tecniche V.I.P. (Vacuum Infusion Process) si avvale di manodopera specializzata, ma anche di pompe, macchine ed impianti volti al controllo costante del vuoto, della temperatura e dell’umidità dei reparti.
Si ottiene, in tal modo, un maggiore grado di tecnicismo che consente risultati più costanti. Una volta che è stato effettuato lo start-up, uno dei primi obiettivi che si raggiunge con l’implementazione di queste tecniche di produzione è la ripetibilità dei pesi delle scocche (che, invece, nel caso di stratificazione manuale può oscillare anche del 5%-10%).
Nella laminazione manuale, infatti, la quantità di resina che viene dosata all’interno delle fibre viene, fondamentalmente, decisa dalla sensibilità dell’operatore che utilizza la pompa di erogazione del mix resina-catalizzatore. In realtà, anche nella laminazione manuale, è possibile effettuare una regolare erogazione della resina: ciò dipenderà strettamente dalla bravura e dall’esperienza degli operatori.
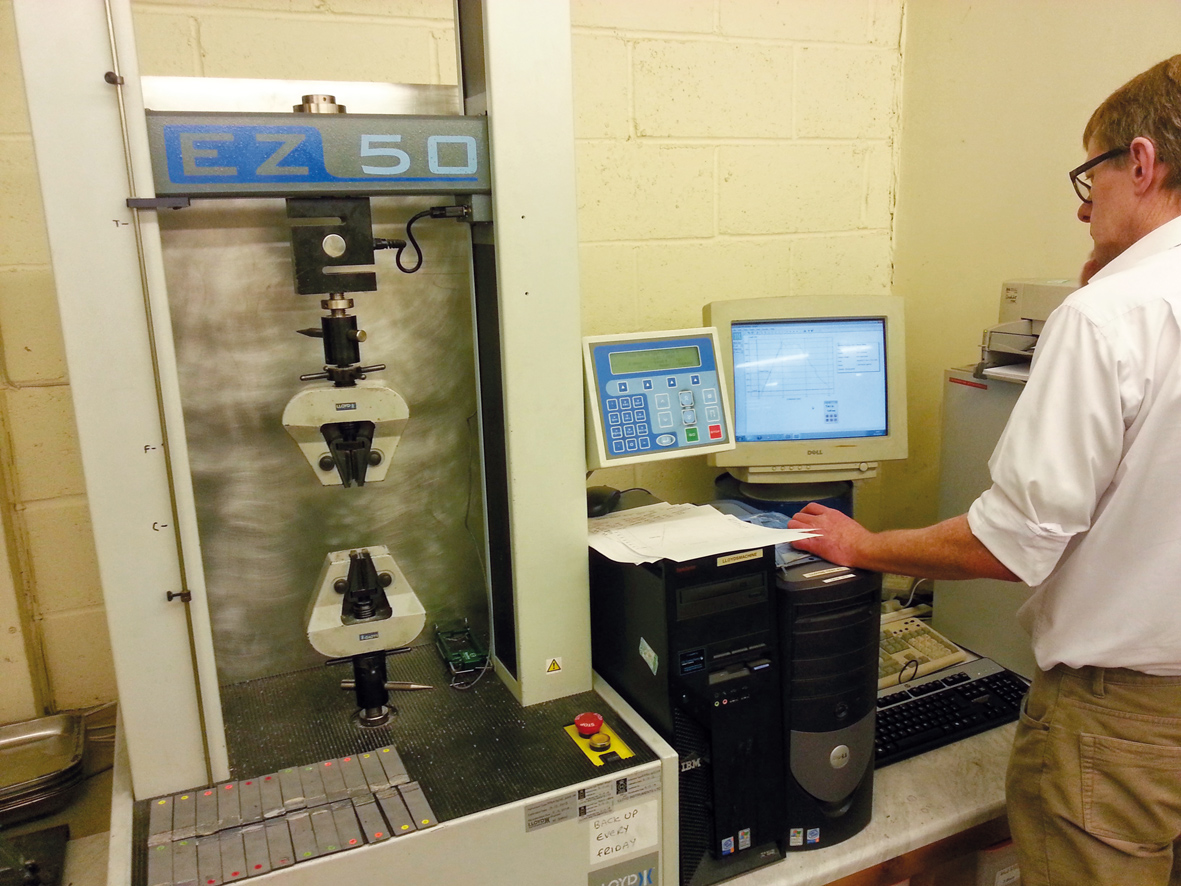
Nelle tecniche sottovuoto, invece, il dimensionamento e la stima del peso del laminato sono molto più “certi” e soprattutto indipendenti dalla perizia dell’operatore, in quanto il volume (e conseguentemente il peso) della resina che penetrerà all’interno delle fibre dell’imbarcazione è rigidamente regolato dai valori di depressione che si ottengono con l’impianto del vuoto meccanizzato.
La pressione esercitata sulle fibre di vetro (o di qualsiasi altro materiale, come anche le fibre di carbonio o aramidiche), con un collaudato e ben progettato sistema di vuoto, equivale a circa 7500/8000 kg su ogni metro quadrato!
Con questo valore di pressione possiamo senza dubbio affermare che la quantità di resina che penetra all’interno del laminato è assolutamente indipendente dall’operatore (perché è funzione dei valori di vuoto) e soprattutto è molto minore se confrontata con la laminazione manuale.
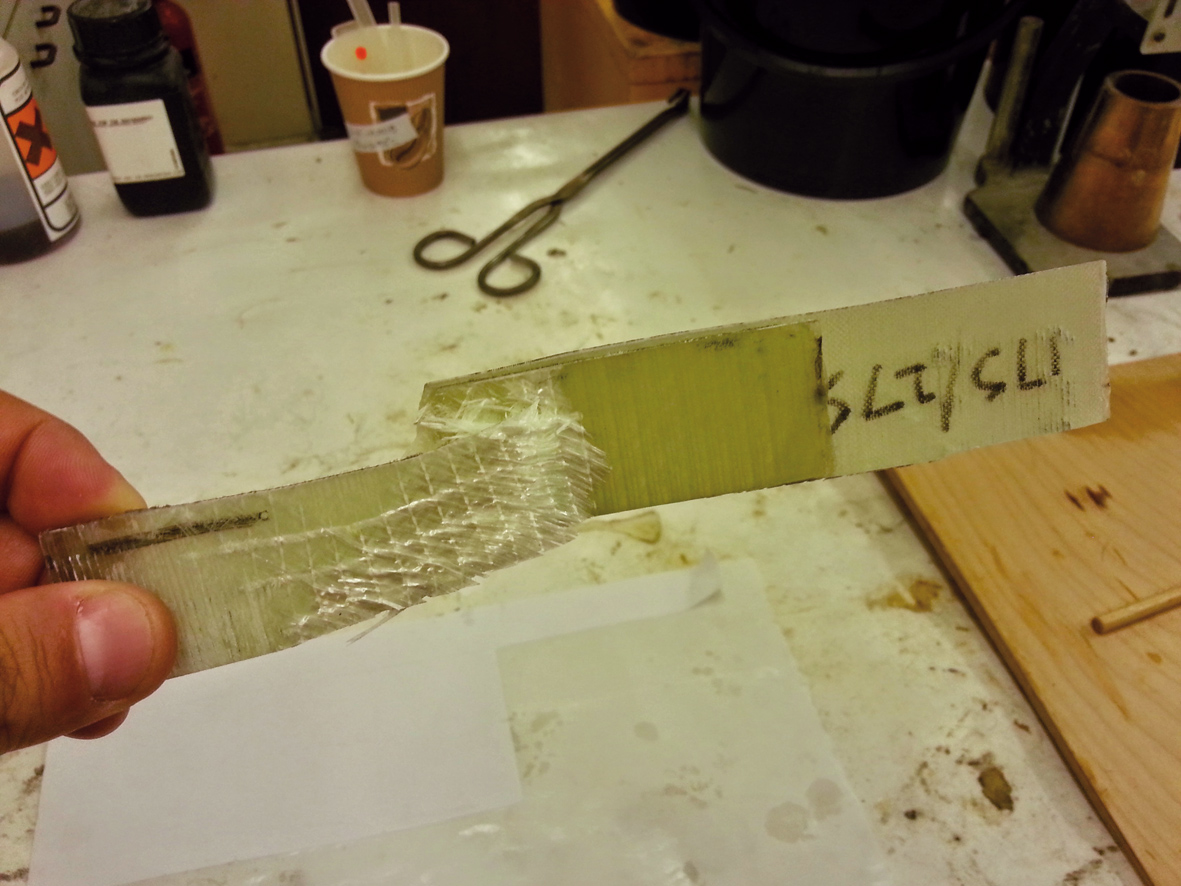
Quindi, il secondo assioma in merito alle tecnologie di costruzione delle imbarcazioni per infusione sottovuoto è legato alla maggiore ripetibilità dei pesi delle scocche e al minore contenuto in resina rispetto alla laminazione manuale.
INCLUSIONI D’ARIA
Terzo punto fondamentale: la laminazione manuale, anche se condotta da operatori esperti, può avere come risultato un laminato con delle inclusioni d’aria. Questo fenomeno, ovviamente, può non essere visibile ad occhio nudo, ma è osservabile attraverso microscopia elettronica a scansione. Le inclusioni d’aria sono, per quanto piccole, considerate difetti che riducono le proprietà meccaniche e pertanto un laminato manuale presenterà (a parità di spessore di un analogo laminato infuso) minori proprietà meccaniche.
Il laminato infuso, infatti, risulta molto meno affetto dall’inclusione di aria. Si ricordi, a tal uopo, che le pressioni di esercizio possono raggiungere anche le sette/otto tonnellate per metro quadrato. Queste pressioni insieme al vuoto costante che viene esercitato lungo le flange degli stampi, naturalmente sono responsabili dell’assenza quasi totale delle inclusioni gassose dell’imbarcazione infusa. Ciò nonostante, una minuta percentuale di inclusioni può essere comunque presente sebbene tendano drasticamente a zero.
Quindi, un terzo assioma postulabile potrebbe essere il seguente: a parità di spessore, un laminato infuso, rispetto ad un laminato ottenuto per stratificazione manuale, presenta proprietà meccaniche superiori almeno del 10-15 % a causa della bassissima presenza di inclusioni gassose rispetto al laminato manuale.
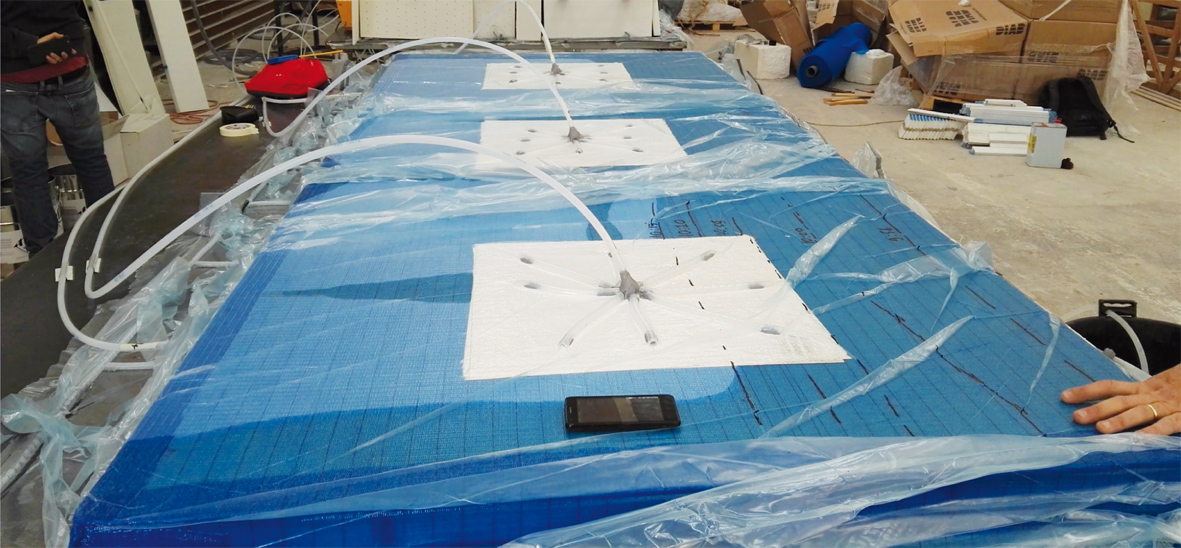
PRECISAZIONI
A questo punto, da bravo “avvocato del diavolo”, e soprattutto quando sembrerebbe che già i primi tre assiomi possano giustificare da soli la presunta superiorità dell’infusione sottovuoto rispetto alla laminazione manuale, vorrei fare, per un attimo, un piccolo passo indietro.
Nel terzo assioma, si postulava che “a parità di spessore…”, ebbene: perché questa precisazione?
Dunque: le tecniche sottovuoto (complice, come al solito, la pressione esercitata) tendono, se l’imbarcazione non è stata progettata appositamente per l’infusione (ebbene sì: ogni progettista quando struttura e dimensiona una barca deve avere ben presente con quale tecnica costruttiva verrà prodotta!), ad assottigliare il laminato.
E questo assottigliamento cosa comporta? Non avevamo affermato che le proprietà meccaniche aumentano in virtù della minore presenza di aria intrappolata?
E’ sicuramente così per quanto riguarda la resistenza alla trazione e ai cicli di fatica, ma per quanto riguarda la flessione dobbiamo fare una precisazione.
Senza voler entrare in un discorso squisitamente ingegneristico, nell’immagine sopra si fa riferimento proprio al concetto che un oggetto di alto spessore è solitamente meno flessibile di un oggetto a basso spessore.
La conseguenza di questo discorso è che un’imbarcazione infusa, sebbene più resistente a sollecitazioni di trazione o di fatica, potrebbe presentare l’inconveniente (a meno che il progettista non abbia sapientemente aggirato questa eventualità) di avere spessori ridotti rispetto ad un’imbarcazione ottenuta per laminazione manuale e conseguentemente essere più flessibile e deformabile sotto l’azione di alcune sollecitazioni.
Come anticipavamo prima, possiamo affermare con sicurezza che all’inconveniente sopra citato si può ovviare con una progettazione “ad hoc” per tecniche sottovuoto.
In altri termini, il progettista esperto conosce bene i pro e i contro di ogni tecnica costruttiva e, al fine di ottimizzarne le caratteristiche, dimensiona l’imbarcazione in maniera “non trasversale”, ossia adotta delle misure specifiche in base all’una o all’altra tecnica di produzione. In questo caso, l’ufficio tecnico che progetterà l’imbarcazione, che sarà costruita con l’ausilio del vuoto, ben conoscendo il problema dell’assottigliamento del laminato, supererà questo ostacolo ricorrendo (solo per fare un esempio, ma le possibilità progettuali sono diverse) ad un dimensionamento di tipo sandwich, ossia predisponendo un’anima di schiuma espansa fra le due pelli di vetroresina.
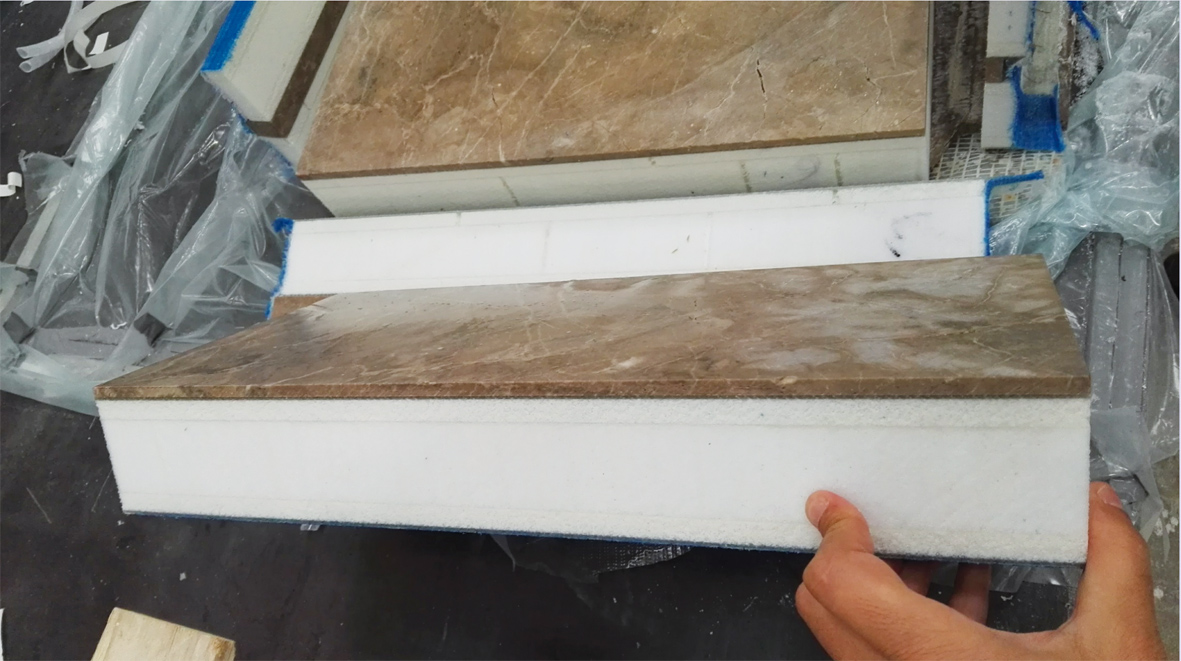
Questo tipo di progettazione, senza l’aggiunta sostanziale di peso (si consideri che un metro cubo di schiuma espansa indicata per questo scopo può pesare, all’incirca, 80 kg), aumenta la rigidezza flessionale e conseguentemente l’imbarcazione risulterà indeformabile anche sotto l’azione di importanti sollecitazioni.
Dunque: proseguendo con il discorso degli assiomi, a valle di questo discorso possiamo affermare il quarto enunciato: un’imbarcazione realizzata in infusione richiede una progettazione specifica rispetto ad una laminazione manuale. Per tale motivo, non è possibile effettuare un trasferimento tecnologico di un’imbarcazione dalla laminazione manuale alle VIP senza rimaneggiare il dimensionamento strutturale della barca stessa.
Vai a “I principi fondamentali dell’infusione sottovuoto – II e ultima parte”