I materiali compositi per l’industria nautica
I materiali utilizzati nell’industria nautica sono, essenzialmente, compositi fibrosi a matrice polimerica termoindurente. I rinforzi fibrosi che vengono impiegati prevalentemente sono essenzialmente di tre tipi: fibre di vetro (di colore bianco), aramidiche (giallastre) e fibre di carbonio (grigio-nere).
I MATERIALI COMPOSITI: LE FIBRE DI VETRO
Nella stragrande maggioranza dei casi, le fibre di vetro sono quelle più adoperate perché, nonostante siano molto economiche rispetto alle più pregiate fibre di carbonio e/o aramidiche, offrono comunque proprietà meccaniche importanti che consentono di ottenere quasi sempre le resistenze desiderate nelle imbarcazioni.
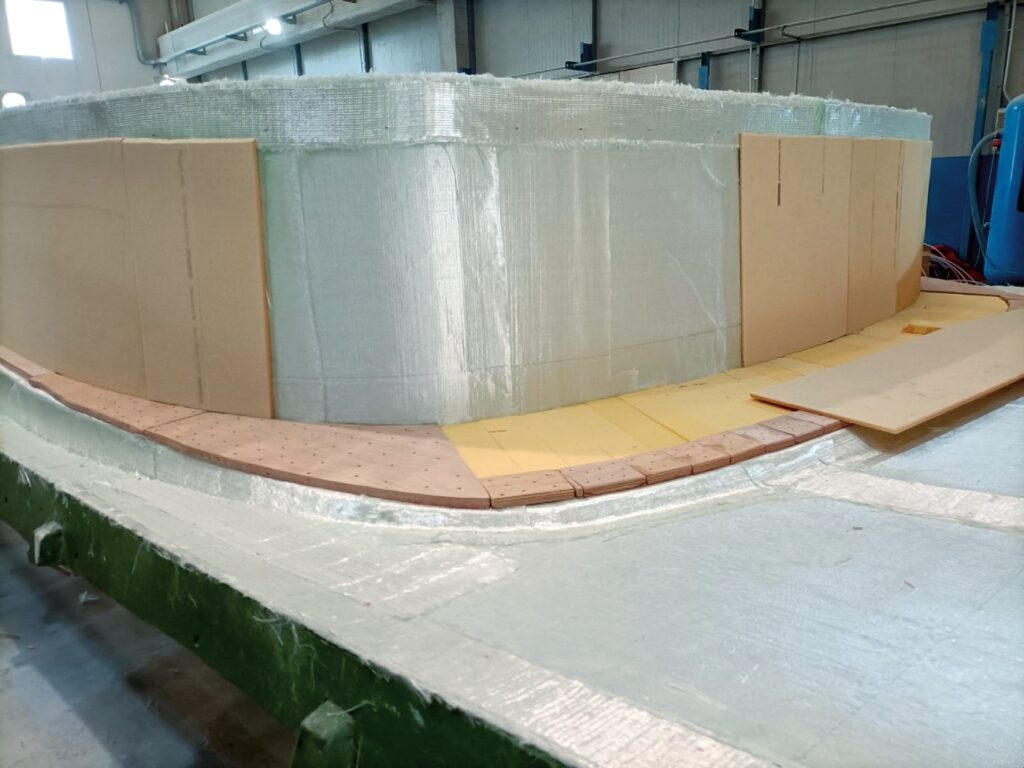
È naturale che, se ci troviamo di fronte alla necessità di costruire qualcosa di estremamente performante come imbarcazioni da competizione o da regata, dove la leggerezza è un parametro fondamentale, bisognerà ricorrere – almeno parzialmente – alle fibre di carbonio e aramidiche, ma, ripeto, nella maggioranza dei casi, le semplici fibre di vetro riescono a coprire quasi tutte le esigenze di progettazione e resistenza strutturale.
In generale (questo lo diciamo per i “non addetti ai lavori”) le fibre sono acquistate sotto forma di “rotoli” di tessuto che possono avere differenti orientazioni e grammature. Da questi rotoli, gli operatori preleveranno le grammature e le orientazioni specificate nel progetto e ne ritaglieranno i vari patch che andranno a costituire il caratteristico “stratificato”.
Nella vetroresina, e in generale in tutti i compositi, le fibre sono le principali responsabili della resistenza del manufatto.
LE RESINE
Semplificando al massimo, potremmo affermare che le fibre supportano i carichi, mentre le resine li trasferiscono. Questo è l’assunto che è sempre stato riportato in molti testi di materiali compositi. In realtà, questa è una semplificazione accademica in quanto la meccanica e la chimica dei compositi sono materie estremamente complicate che richiedono un’importante know-how tecnico e un’esperienza profonda per comprenderne e prevederne i comportamenti che sono estremamente variabili e complessi.
A ogni modo, per tenere insieme le fibre e consentire quindi che funzionino, c’è bisogno di un legante, per l’appunto, rappresentato dalle resine. Nei materiali compositi per la nautica, le fibre possono essere annegate in vari tipi di resine polimeriche. Vediamo quali sono. Premetto che, siccome questo articolo non è una pubblicazione scientifica, ma vuole semplicemente divulgare contenuti tecnici a tutti i lettori, come sempre andiamo al nocciolo della questione e facciamo riferimento alle due famiglie di resine principali che vengono utilizzate nei cantieri nautici.
Le resine poliesteri
La prima grande famiglia di resine è rappresentata dalle resine poliesteri, che hanno, al loro interno, tre sotto-categorie. All’interno di questa classe possiamo trovare resine di bassa qualità denominate ORTOFTALICHE (fortunatamente poco utilizzate nella nautica industriale), resine con caratteristiche intermedie (le cosiddette ISOFTALICHE) e resine con ottime proprietà chimico-meccaniche che possono essere utilizzate anche per oggetti di pregio e prodotti hi-tech (le resine VINILESTERI).
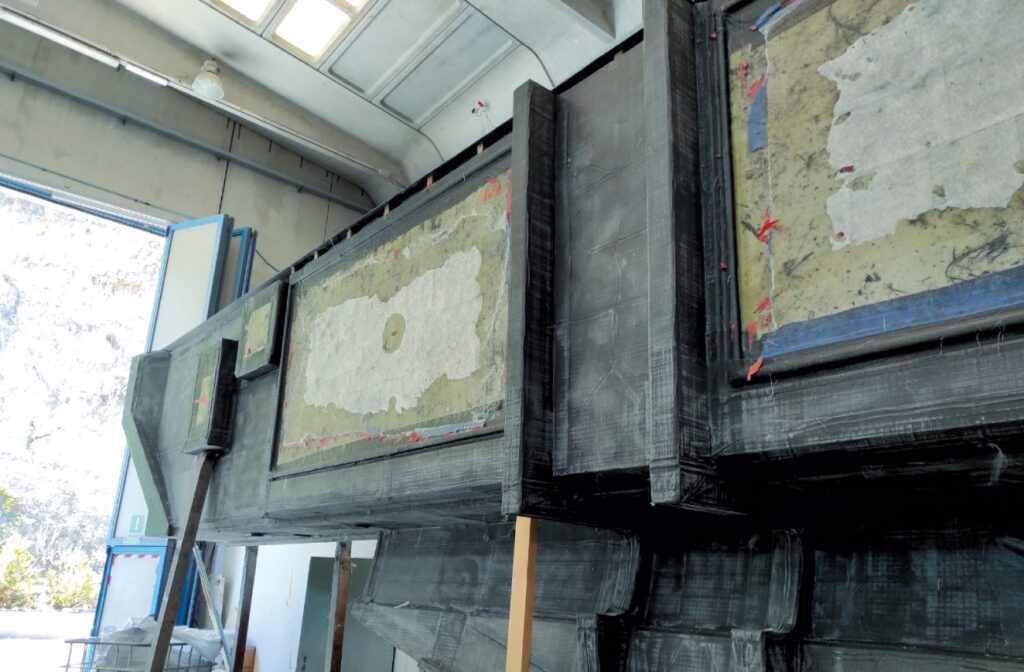
Le resine epossidiche
Alla seconda famiglia di resine, invece, appartengono le EPOSSIDICHE che – generalmente – hanno proprietà chimiche e meccaniche buone (superiori rispetto alla media delle resine poliesteri), ma possono essere lavorate solo a determinate condizioni di temperatura e umidità perché rispetto alle resine poliesteri risultano più sensibili alle condizioni ambientali.
Quindi, abbiamo capito innanzitutto che i materiali compositi con cui si costruiscono le barche sono costituiti da fibre di vetro (nella maggioranza dei casi), fibre di carbonio e aramidiche (di solito utilizzate per sovrastrutture, elementi che richiedono leggerezza estrema o barche da competizione) e resine poliesteri (con l’impiego prevalente di ISO e VNL) o epossidiche. Non è finita, però.
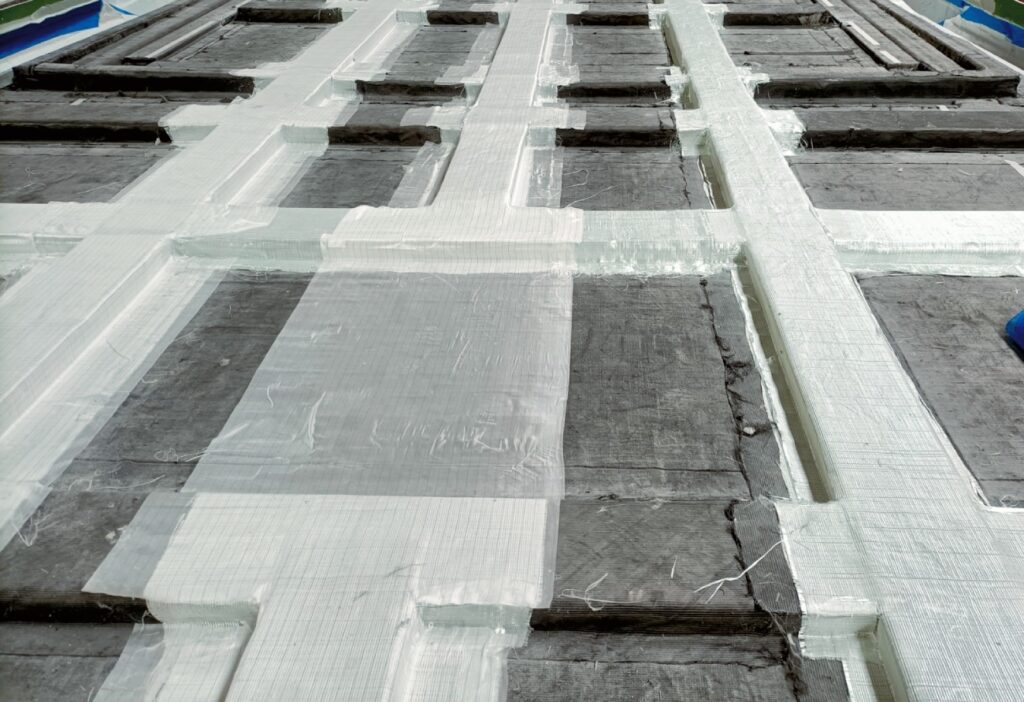
ALTRI MATERIALI
Le scocche delle imbarcazioni non sono costituite solo da resine e fibre mescolate insieme. All’interno di questo “mix”, in realtà, vengono inseriti diversi altri materiali che, sebbene siano veramente tanti, sintetizziamo a seguire in altre due o tre categorie.
I Gelcoat isoneopentilici
La prima cosa che viene applicata su uno stampo dal quale si produrrà l’oggetto è il colore dell’imbarcazione. Nei compositi, infatti, il colore viene applicato prima di iniziare il processo di costruzione vero e proprio. Il colore è il pigmento presente nel Gelcoat che, fondamentalmente, altro non è che una resina pigmentata. La maggior parte dei Gelcoat prodotti al giorno d’oggi è di natura Iso Neo Pentilica e risulta – pertanto – compatibile con le resine ISO-VNL (le due sottocategorie della prima famiglia). I Gelcoat isoneopentilici, che esistono in svariati tonalità e colori (inclusi metallizzati), sono – purtroppo – poco compatibili con le resine epossidiche in quanto lo stirene contenuto nel materiale ne provoca il distacco, per cui con la seconda famiglia di resine bisognerà mettere in campo diversi accorgimenti (di cui parleremo in un articolo dedicato).
Le schiume polimeriche: PUR e IPN (o PVC)
Un’ultima categoria di materiali a cui vogliamo fare riferimento in questo editoriale sono le schiume polimeriche che, di solito, possono essere principalmente di due tipi: PUR (schiume di poliuretano) e IPN (schiume di polivinilcloruro).
Le schiume di PUR, generalmente, vengono impiegate per dare la forma allo scheletro dell’imbarcazione, ossia ai longheroni e ai madieri. Sono generalmente leggerissime (un metro cubo pesa all’incirca 35 kg), ma hanno proprietà meccaniche molto basiche. Per tale motivo, l’industria nautica le utilizza prevalentemente per fornire la sagomatura del progetto alle strutture di scafi e coperte.
Le schiume di IPN (o PVC), invece, contribuiscono effettivamente alla strutturalità del composito e vengono inserite all’interno del laminato con lo scopo di aumentarne esponenzialmente le proprietà meccaniche senza inficiarne la leggerezza finale (si consideri che un metro cubo di PVC può pesare mediamente dagli 80 ai 200 kg, per cui parliamo comunque di prodotti con un peso specifico estremamente basso). Le schiume di PVC nei laminati dei materiali compositi vengono inserite a mo’ di distanziatori delle pelli, emulando – essenzialmente – il concetto di scienza della costruzione della trave a doppio T.
Il PET
Un’ultima categoria estremamente interessante, che si sta facendo strada nel mondo dei compositi (e conseguentemente attenzionata anche dall’industria nautica), è quella delle schiume di PET.
Il PET è, praticamente, uno dei materiali con cui si realizzano anche le bottiglie di plastica. Alcune schiume, anzi, vengono realizzate proprio con scaglie di riciclo di queste bottiglie. La Diab, ad esempio, è uno dei più grossi produttori che propongono schiume di PET prodotte con scaglie di materiale riciclato. Le schiume di PET hanno diversi vantaggi. Possono essere “sagomate” come il PUR (e quindi utilizzate per dare la forma a longheroni e madieri), ma – a differenza del PUR che ha proprietà scadenti – hanno caratteristiche meccaniche molto interessanti (generalmente inferiori solo del 20% rispetto alle schiume di PVC) e per tale motivo, oltre a dare la forma, possono essere inserite all’interno dei calcoli dei progettisti perché contribuiscono alle proprietà meccaniche del composito.

In ultimo, ma non per importanza, sottolineerei il carattere estremamente eco-friendly del PET e la sua “sostenibilità”. È indubbio, infatti, che il prossimo futuro dell’industria nautica vedrà approfondire con sempre maggiore attenzione tutti gli aspetti legati al “green” e alla “sostenibilità ambientale” affinché anche questo settore si adegui alle necessità del mondo moderno e agli obiettivi dell’Agenda 2030.