Si fa presto a dire vetroresina: le fibre usate per costruire imbarcazioni
Alcuni diportisti non immaginano che nelle imbarcazioni di vetroresina non sono presenti esclusivamente (come la parola suggerirebbe) fibre di vetro e resina.
Al contrario, il materiale che le costituisce può essere estremamente variegato, in quanto “composito” ossia composto da più fasi e diversi sottotipi di elementi.
Abbiamo visto nei precedenti editoriali che sebbene le fibre di vetro siano le più gettonate (per un fattore di resistenza rapportata al costo d’acquisto), non è raro trovare nel diporto inserimenti di fibre aramidiche (comunemente chiamate “kevlar”, sebbene quest’ultimo sia il nome commerciale di questo tipo di rinforzo) o tessuti di carbonio.
Tutto questo, chiaramente, incide sui costi di produzione, ma – in qualche maniera – ha un ritorno in termini di benefit tecnici e di confort di navigazione.
L’adozione di fibre “non convenzionali” non è, infatti, un vezzo o una moda. L’uso di fibre super resistenti consente all’armatore di manovrare, essenzialmente, un’imbarcazione più leggera, più resiliente agli urti e sicuramente più economica in termini di consumo carburante.
Cosa comporta l’adozione di fibre speciali?
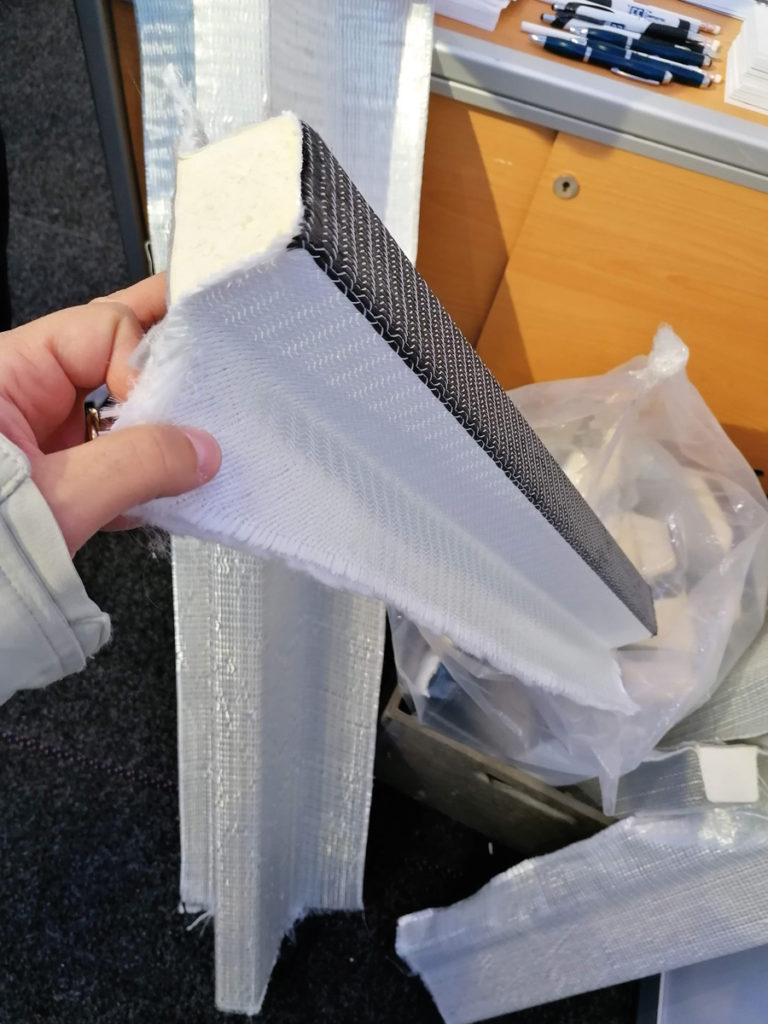
alla resistenza meccanica dell’imbarcazione
È chiaro, come dico spesso quando mi confronto con i tecnici di cantiere, che fibre speciali non possono essere “amalgamate” da resine comuni. Chi lavora il carbonio o il kevlar dovrà adottare anche delle resine dalle particolari proprietà chimico-fisiche e meccaniche.
Una delle prime cose che mi saltano all’occhio quando conduco un survey è, infatti, proprio l’adozione di resine inadeguate per un particolare tipo di fibra. Cerco di essere più chiaro. Usare un rinforzo in carbonio impregnato con resina comune è come mettere benzina agricola in una fuoriserie.
Nella struttura dell’imbarcazione la parte resistente, infatti, è rappresentata proprio dalle fibre, ma il trasferimento dei carichi è assolutamente demandato alle resine.
A tale scopo, non bisogna dimenticare che queste ultime sono suddivise in famiglie e ognuno di questi sottotipi esibisce delle proprietà differenti a seconda della natura chimica dei singoli “anelli” che costruiscono la catena macromolecolare.
Parole apparentemente difficili che ci fanno comprendere che ogni resina può avere delle differenze anche sostanziali, a seconda di come viene formulata.
Quali resine scegliere?
Per questo motivo, dovranno essere sempre privilegiate resine a basso coefficiente di assorbimento d’acqua e minimo ritiro, quando si tratta di costruire imbarcazioni di un certo tipo e a maggior ragione se i rinforzi fibrosi saranno più pregiati rispetto al vetro tradizionale.
Difatti, se una resina assorbe acqua, il laminato ne risulterà minato e – conseguentemente – anche laddove fossero state impiegate fibre estremamente costose e resistenti, il loro utilizzo verrebbe vanificato, in quanto i carichi non verrebbero trasmessi (e quindi sostenuti) adeguatamente.
I “cores”
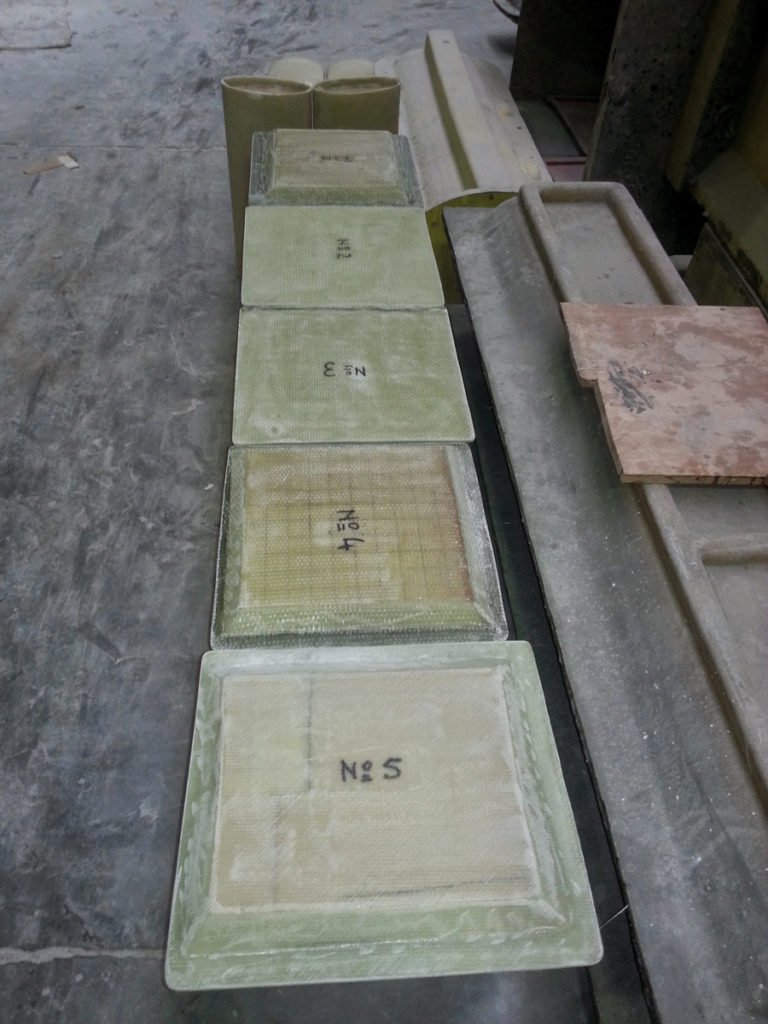
Discorso a parte, invece, per tutti i “cores” che possono essere impiegati all’interno del laminato.
Si intende per “core” un materiale d’anima che viene frapposto fra due pelli di vetroresina (e/o carboresina e/o aramiresina) in modo tale da distanziarle e (in soldoni) aumentare la rigidezza flessionale.
Il materiale d’anima, in pratica, agisce sulla resistenza alla flessione del laminato senza gravare sul peso dello stesso.
Questo parametro è fondamentale per avere dei manufatti che non deflettono in maniera anomala sotto l’azione dei carichi e lo è ancor di più, con alcune tecnologie di produzione che hanno l’effetto di “assottigliare” i laminati. Mi riferisco, chiaramente, all’infusione e a tutte le varianti delle tecnologie sottovuoto, che hanno come controindicazione tecnologica proprio quella di “appiattire” le fibre sotto l’effetto del vuoto. In tal modo, i generici pannelli di fasciame di carena o coperta possono assottigliarsi, risultando – perciò – più soggetti alla deformazione e alla flessione.
Per questo motivo, soprattutto quando in un cantiere si adottano tecnologie sottovuoto, non è indicato progettare esclusivamente con laminati pieni (costituiti solo da fibre e resine), ma è consigliabile dimensionare strutturalmente col sandwich e inserire delle anime di schiuma espansa ad alto spessore e basso peso specifico (in modo da non incidere sul peso), che aumentino la resistenza flessionale delle imbarcazioni.
In realtà, le schiume di IPN o di PET non hanno come beneficio solo quello di aumentare la resistenza alla flessione. Esse, infatti, contribuiscono all’isolamento termico ed acustico delle imbarcazioni e dei relativi ambienti.
Conclusioni
Siamo negli anni 2020. La vetroresina di 30 o 40 anni fa ha lasciato il posto ad un vero e proprio materiale composito, costituito da diversi tipi di materiali che coniugano insieme diverse proprietà meccaniche e chimico-fisiche.
Le poche imbarcazioni che ancora vengono realizzate esclusivamente con fibre di vetro e resina sono ormai un po’ datate in termini tecnici. Probabilmente sovradimensionate, lente e pesanti.
Saper scegliere con cura i materiali, costruire “ad hoc” un laminato e produrlo a regola d’arte garantisce al cliente finale la fruizione di un mezzo performante, resiliente e meno impattante sui consumi di carburante.